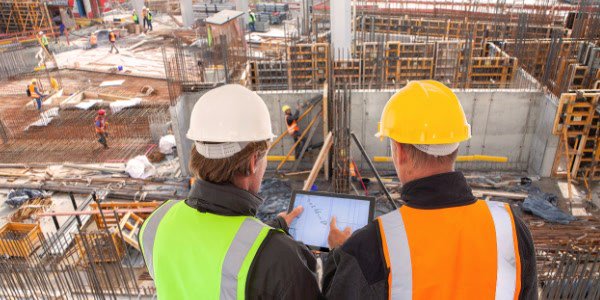
As owners and architects search for building solutions that are greener, provide a lighter footprint, reduce the need for finish materials, and speed up construction, mass timber construction has joined the cutting edge of design and construction.
What is mass timber?
Scientists recently discovered evidence that humans first built wooden structures 476,000 years ago.1 Within this long history of wood construction, mass timber technology is fairly new, especially in the US. For comparison, Europe is home to 60 of the world's 84 mass timber structures that are at least eight stories tall.2
Mass timber construction uses engineered wood products instead of steel and concrete as structural members. These products are generally assembled from individual pieces of kiln-dried lumber. Examples include Glulam, which are laminated wood pieces where the grain runs in the same direction, and cross-laminated timber (CLT), where the grain runs at right angles to each other. Glulam is often used to construct beams and columns, while CLT is used to form sheets to form floors and walls. Mass timber panels can also be assembled by joining wood pieces with dowels (DLT) or nails (NLT). Mass timber can also be made of waste wood assembled into plank-like shapes.
Mass timber should not be confused with traditional light wood framing, where a building may be constructed using 2x4s or similar pieces of individual lumber. One significant difference between two kinds of construction is that mass timber is used for structural support, it can also be used for other building elements, such as walls and flooring.
From a structural perspective, mass timber can be used to build much larger structures than light wood framing. For example, Portland Oregon's airport will soon be sporting a 380,000-square-foot mass timber roof.3 In Maine, mass timber was recently used to construct a 46,000-square-foot building at Bowdoin College that includes a 300-person event space.4
While mass timber can be used for long spans, designers may need to use double beams and higher-than-normal buildings to accommodate greater beam depth.
Advantages of mass timber
Mass timber is appealing for a number of reasons. First, because it's made from wood, it has a much lower carbon footprint than steel and concrete. Mass timber can also be made from wood that might otherwise go to waste, such as wood from trees killed by beetle infestations or destroyed by natural disasters. It is also lighter, allowing for lighter building foundations.
From an architectural point of view, wood is a warmer material, and architects will often leave mass timber structural elements exposed for aesthetic reasons. This technique reduces the need for other finishes like drywall and paint, which eliminates some sources of volatile organic compounds (VOCs). Open spaces, however, can require designers to identify alternatives for ducted heating, ventilation and air conditioning (HVAC) systems, because ducts aren't usually considered aesthetically pleasing.
Mass timber needs to be prefabricated off-site, which can decrease on-site building time. The time to form and pour concrete restricts the speed with which a concrete structure can be built to about one floor every seven days, but a mass timber structure can be raised in as little as one day per floor. In one recent library project, the contractor was able to erect a building enclosure using CLT for the primary and secondary structures in just three days.5 An Army study found that a mass timber hotel at the Redstone Arsenal was constructed 20% faster than comparable hotels, using 44% fewer personnel hours.6
Demand for mass timber
The current sweet spot for CLT is in mid- to high-rise buildings, which can't use light-gauge metal stud or masonry unit construction. Examples of mass timber structures include an 184,000-square-foot, five-story office building in Tempe, Arizona7 and a 19-story apartment building in Oakland, California.8
Interest in mass timber is best demonstrated by a recent mandate from the Army Corps of Engineers (USACE) that all vertical construction projects consider mass timber and cross-laminated timber in design.9 USACE's direction is largely focused on the environmental benefits of mass timber, but it also finds efficiencies in mass timber construction. Given the speed and other advantages of mass timber construction, we can expect to see much more construction, but it will take time for more manufacturing capacity to come online and for contractors and code officials to gain experience with the product.
Mass timber risk factors
Because mass timer is a relatively new material, it's difficult for insurers — especially in the US — to evaluate the risk of mass timber when issuing builder's risk and then property insurance policies. As a result, it's often difficult to place insurance on a mass timber structure, and that insurance often comes with sticker shock. To address these issues, it's important to address the most significant risks at the planning stage.
The greatest risk during construction involves water and moisture. Until the mass timber elements are placed and the building is dried in, mass timber elements are subject to damage from water, much of which is just aesthetic damage. Accordingly, when designing and constructing a mass timber structure, the parties need to consider and plan for:
- How to protect the timbers from water between the time they leave the manufacturer's care until they're placed in the structure
- Lead times for re-manufacture in the case of damage
- Temporary measures during construction to protect the timbers from water until the building is dried-in
- How water will be removed if the timbers are exposed prior to dry-in
Another exposure is the risk of fire. Many insurers assume that mass timber burn in the same way that light wood framing burns, but that's not the case, because the timbers are assembled in larger pieces using fire-resistant glues. Indeed, some evidence shows that mass timber can actually perform better in a fire than steel, as steel can become plastic within an hour, but exterior charring on the mass timber doesn't materially affect its structural capacity.10
At the Bowdoin College Project in Maine mentioned above, the contractor addressed some of these insurance concerns by adding:
- Digital and wireless security
- Water, fire and smoke monitoring
- Motion sensing systems4
It's also important to engineer the building to prevent the spread of fire both during and after construction. When evaluating a risk, insurers often look at the Estimated Maximum Loss (EML) that may occur in the event of a specific risk. In a typical high-rise fire with non-combustible concrete decking, the insurer may assume that a fire on one floor will result in a complete loss of that floor, smoke damage on the next floor or two and water damage to the floor below, resulting in an EML of four floors.
With mass timber, CLT floors may be considered combustible, with the assumption that fire can spread to upper floors, leading to a greater EML. To reduce the premiums, it's essential to explain how a fire will be prevented from spreading to the upper floors. After the building is turned over, sprinklers may address this concern, but contractors and engineers should also consider how a fire will be stopped before the fire protection system becomes active.
Building challenges with mass timber
Some of the largest mass timber challenges come from an overall lack of experience with mass timber construction. Contractors in the US generally don't have significant experience with mass timber. Indeed, although Europe is the clear leader in the mass timber construction market, European builders also struggle with a lack of industry expertise to deliver mass timber buildings. A side effect of this lack of experience is an increased risk of construction defect claims from improper workmanship and a risk of delays as project managers learn to manage mass timber procurement.
A similar challenge is that building officials also lack experience with mass timber construction, which can lead to greater code scrutiny.
Because mass timber building elements are fabricated off-site, planning is required to ensure that each piece is properly fabricated. Off-site fabrication can be a disadvantage because workers may be unable to make field modifications to adjust for fabrication errors. While a steel worker can simply drill new holes for a connection, on-site modifications may not be possible with mass timber.
Another challenge, both in the US and Europe, is the lack of manufacturing capacity for mass timber. However, the number of CLT manufacturers in the US has expanded dramatically in recent years, with at least eight known manufacturers and at least one foreign manufacturer constructing a facility. While most of these facilities are clustered in the Pacific Northwest, manufacturers are also found in the Plains states, as well as a new facility located in North Carolina. However, supply constraints on mass timber certainly exist both in the US and in Europe.
Finally, because mass timber elements need to be manufactured off-site to exacting tolerances, there's also a concern about long lead times to replace damaged elements, which can lead to greater Builder's Risk claims. When procuring Builder's Risk insurance for a mass timber project, the design and construction teams will need to work closely with your broker to explain their approach to addressing these risks.
Conclusion
Mass timber construction is still in its infancy, especially in the US. But, there are clear reasons to believe that it will become much more common. Mass timber provides a much-desired carbon sink, allows for rapid construction and can provide cost savings not just in time but also in a reduced need for finish materials because the structural wood product can also serve as a finish.
Current challenges should decrease as designers, contractors and code officials become more familiar with the product and insurers gain a greater understanding that mass timber isn't light wood framing, but instead an entirely different product.
Gallagher has invested a lot of time and resources in understanding the mass timber/CLT market sector. We've met with global experts to help develop an insurance approach that more closely reflects the unique characteristics of mass timber CLT versus just considering it "wood frame." This effort continues to develop, but already has resulted in partnering with key carriers to provide more specific pricing and coverage terms instead of just lumping it into the wood frame models.
We'll continue to pursue these efforts to grow this market segment that benefits owners, contractors and end users.