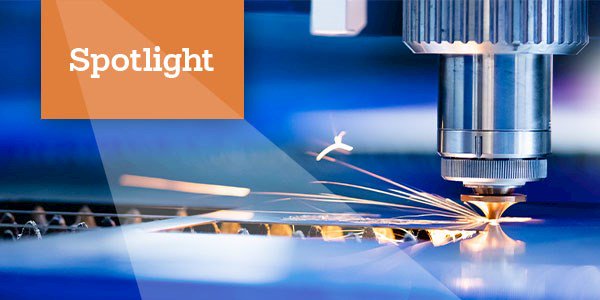
Over-reliance on single-source supply chains can present significant challenges in a polycrisis world.
Consider the case of Taiwan, which produces more than 90% of the world's most advanced semiconductors, integral to nearly every digital device.1 Chip shortages in 2021 had a dramatic impact on production of high-tech products. For example, the auto industry produced eight million fewer vehicles when supplies fell short, shaving an estimated $240 billion off the US gross domestic product (GDP) that year.2
Subsequent events have affected Taiwan's chip production, including a 2023 drought that reduced the availability of water for cleaning silicon wafers and a 2024 earthquake that forced major semiconductor manufacturers to evacuate. Recent escalations in geopolitical tensions between China and Taiwan have the potential to trigger additional disruptions.
Meanwhile, backlogs at key shipping routes, such as in and around the Suez Canal, are slowing the flow of semiconductors to importing countries. "Cargo owners, shippers and ship owners are making the decision on whether to continue shipping through the area," says Alec Russell, executive director of Marine Cargo at Gallagher Specialty.
Onshoring and near-shoring solutions
To mitigate the impact of supply chain interruptions, some manufacturers have increased their investment in onshore and near-shore production or are considering moving manufacturing to countries where the goods are sold.
As a result, for the first time in two decades, American manufacturers now purchase more goods from nearshore countries such as Mexico than from China.3 For example, Apple spent $16 billion to diversify production assets from China, including major investments in Mexico, India and the US.4 And MIT Sloan Management Review reported that "companies are building manufacturing facilities in the US at a pace not seen in decades," with construction increasing by 40% over recent years.5
Meanwhile, more than half of UK manufacturers have efforts underway to reshore supply chains.6
"Aligning business strategy with supply-chain design is one way to reduce vulnerability," says Chris Demetroulis, managing director of Transportation at Gallagher.
The lure of low overseas labor costs may have initially created the demand for offshoring, but advancements in automation and artificial intelligence (AI) have streamlined many manufacturing processes, bringing greater efficiency to the process.
And what about those semiconductors? Taiwan Semiconductor Manufacturing Company (TSMC) is diversifying with new plants in the US, Japan and Germany, to bring the supply of chip components closer to manufacturers.7 Other companies are following suit. And the White House is supporting the effort to reduce dependence on Taiwan for chips: The US CHIPS and Science Act8 has committed $166 billion in investment in semiconductors and a further $5 billion in research to spur innovation.9
"This generational shift is the second great industrial disruptor in the 21st century after e-commerce," comments Lisa DeNight, managing director, National Industrial Research at Newmark.10
Pros and cons of onshoring and near-shoring
Near-shoring and reshoring have numerous benefits, including:
- Shortened supply chains
- Less concern about supply chain blockages
- Greater control over production
- Faster response to market fluctuations and demand
- Reduced shipping and transportation costs
All of these mitigate risk, especially when reducing reliance on product-dominated locations. There can also be positive brand messaging for products made in home countries rather than overseas.
Manufacturers investing in near-shoring and onshoring are also leveraging circular economy efficiencies, reusing materials in production with reduced logistics costs.11
There are challenges, however, including:
- High costs for labor in some countries
- Limited infrastructure to support manufacturing
- Skilled labor shortages in some locations
- Requirement for new supply chains
A comprehensive risk management strategy
Localized and nearby supply chains allow manufacturers to recover more quickly from disruptions, reducing their impact. As manufacturers decouple long-standing relationships to diversify suppliers and bring manufacturing closer to home, they're de-risking vertical supply chains.
Onshoring and near-shoring are part of a broader risk management strategy. As companies continue to assess their risk profile, taking a comprehensive examination of operational, financial, and strategic risks is essential.
Businesses should approach risk management services as strategic partners who can help guide high-level decisions. Traditional risk management was often viewed as a compliance function. Resilient companies build risk management in decision-making with an adaptive risk governance model that evolves along with the risk landscape.
Published July 2024